This week we have the final part of Project Conservator Mhairi Boyle’s series on the conservation treatment of three Percy Johnson-Marshall architectural models. The first part can be read here.
Putting the Pieces Together: The Challenges of Working on Architectural Models (Part 2)
In my last blog, I introduced the Percy Johnson-Marshall architectural models, and the challenges faced when designing a treatment plan for them. In this week’s blog, I am going to tackle the topic of different adhesives and treatment methods used in this project.
In the field of paper conservation, there are a few gold-standard adhesives. The most ubiquitous adhesive that almost all paper conservators use is wheat starch paste. Though most conservators associate starch-based adhesives with East Asian conservation practices, one of the earliest recorded uses for starch was recorded in Ancient Egypt, where it was used to adhere pieces of papyrus together.
Powdered wheat starch mixed with water over heat forms a gelatinous paste, which can be tailored to suit different purposes. It can be kept thick (‘dry’), or thinned out with more water. Dry paste is often used to mend thicker paper-based objects or objects which cannot tolerate a lot of moisture, and thinned out paste is used when more flexibility is required. I decided to use a very dry paste to attempt to re-adhere lifting areas of the models, with varying degrees of success. Wheat starch paste requires at least 10-15 minutes to dry, meaning that the part of the object being repaired with paste needs weighted down. Although wheat starch paste is a strong and reliable adhesive, the extent of the water damage and the embrittlement of the card used in areas of the model meant that it was not strong enough to re-adhere parts of the model.
Collections Care Assistant Sarah Partington and I then moved onto using EVA glue. EVA stands for ethylene-vinyl acetate. It is a synthetic adhesive that was adopted by conservators in the 1980’s as a more reversible (but still challenging to remove) alternative to the completely irreversible PVA (poly-vinyl acetate). EVA is commonly used
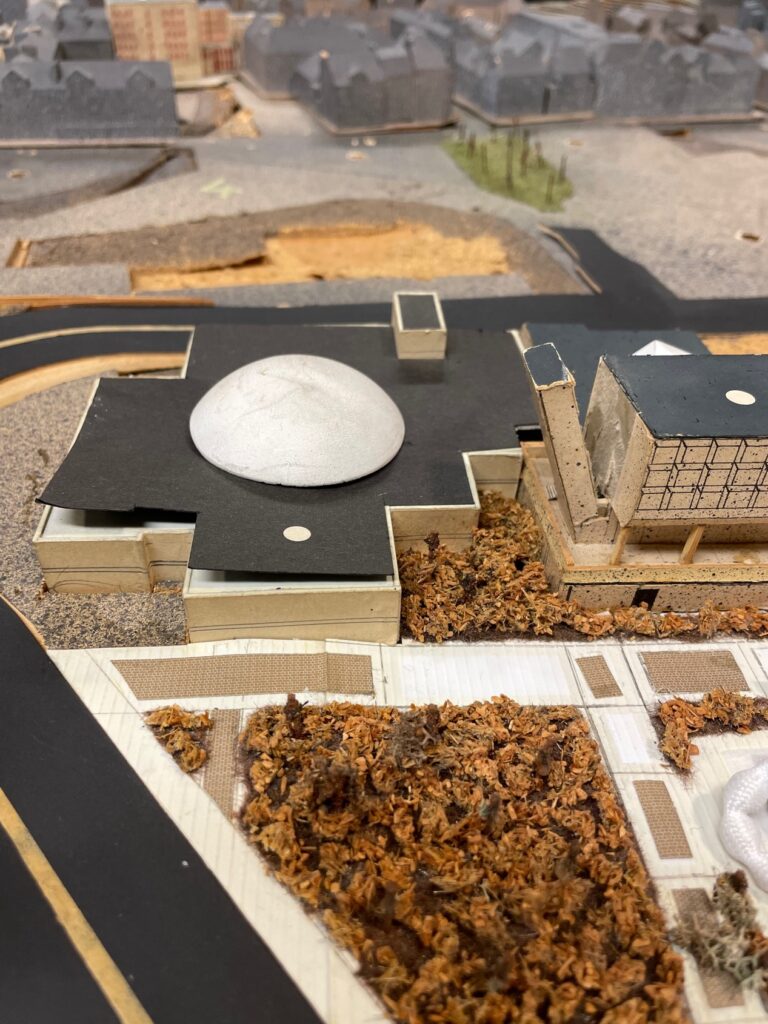
Loose and lifting areas of one of the models.
in book conservation and artefact conservation. It’s stronger than wheat starch paste, but also has a longer ‘curing’ time. Rather than ‘drying’, adhesives like EVA and PVA react with the environment and form flexible solids.
Using EVA worked in some cases, but again, the drying time was not quick enough for the thicker cards used on the model. We also found that the weights we were using during the drying process were not quite the right size. At this stage, I turned to our Musical Instruments Conservator Jonathan Santa Maria Bouquet for some assistance.
Jonathan has experience dealing with an incredibly dynamic collection of 3D objects, chiefly musical instruments, and his workshop reflects this. Whereas paper conservators often have nimble and petite tools in their arsenal, Jonathan has saws, drills, clamps, and hammers.
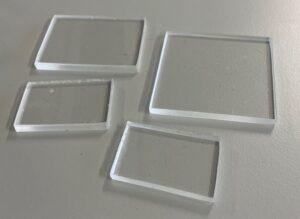
Custom acrylic weights made by Jonathan Santa Maria Bouquet.
He very kindly lent Sarah and I some clamps to hold areas of the models in place while drying and created some custom-shape acrylic weights for us to use.
In addition to this, Jonathan suggested we try the adhesive Paraloid B72. B72 is an acrylic resin which has been used in conservation for over 25 years, and is commonly associated with archaeological and objects conservation. It is manufactured as small hard pellets which are then dissolved in a solvent of choice. Solvents are chosen based on how quickly they evaporate and their compatibility with the object – the quicker a solvent dissolves/dries, the quicker the adhesive will dry. Jonathan recommended a 50/50 mix of acetone and isopropanol, to give a medium-fast drying time.
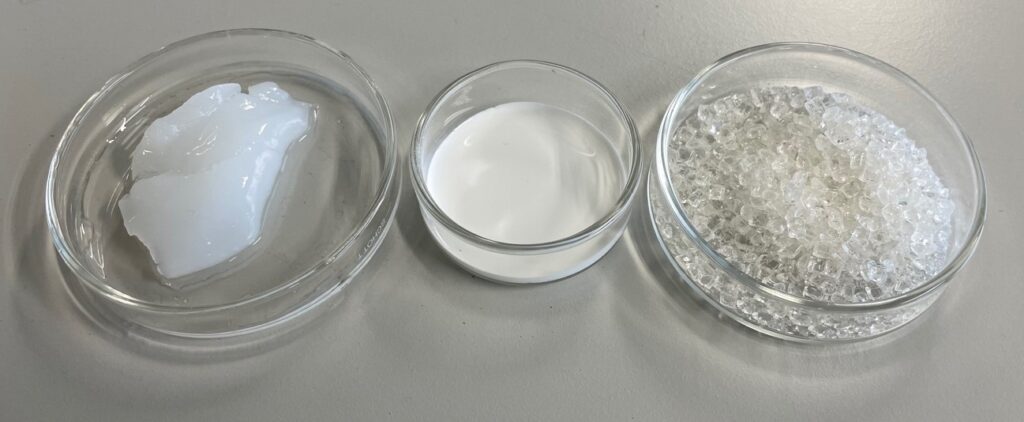
From left to right: wheat starch paste, EVA, and Paraloid B72.
The B72 was a success – in conjunction with the custom weights and clamps, Sarah and I managed to successfully adhere all loose components of the models. It dried quickly, and the clamps and custom weights allowed us to apply a stronger and more precise amount of pressure to drying areas.
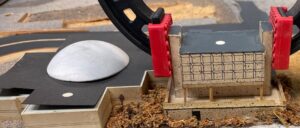
Clamping an area of the model to allow the Paraloid B72 to dry.
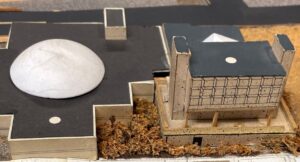
Successfully re-adhered components.
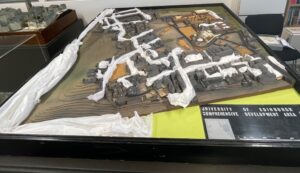
Acid-free tissue was built up to create an even plane, reducing the risk of pieces coming loose.
After the models were made secure, Senior Collections Manager Katharine Richardson and I met to discuss the safe packing and moving of them. Sarah and I prepared for their move by covering them in acid free tissue, filling in any gaps between built-up areas so that they wouldn’t come loose and knock against each other. The external removals contractors then arrived, and we discussed the safest method of moving the models. Large plastic bags were used to cover the models and tissue, and everyone held their breath as the largest model was tipped on its side to fit through the door.
Everything remained secure, and the models made it safely to the University Collections Facility. This project demonstrated the importance of cross-disciplinary collaboration and wouldn’t have been possible without the whole team mucking in to put the pieces together.
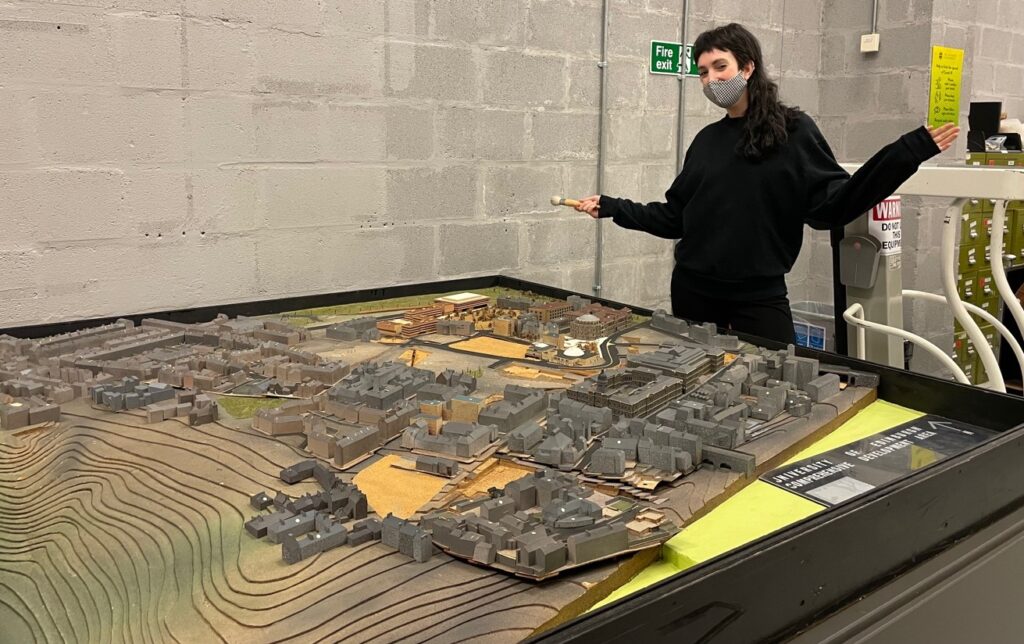
Sarah and one of the models, all in one piece!
Further Reading:
Whitten, J., Buckley, B., Houp, H., Vagts, L., Irgang, H., van Gelder, M., Blakney, S., Roth-Wells, N., & Pocobene, G. 1997, Varnishes and Surface Coatings: Polymeric Varnishes, https://www.conservation-wiki.com/wiki/Varnishes_and_Surface_Coatings:_Polymeric_Varnishes
Koob, SP. 2009, ‘Paraloid B-72: 25 Years of Use as a Consolidant and Adhesive for Ceramics and Glass.’, in Ambers, J., Higgitt, C., Harrison, L., & Saunders, D. (eds) Holding It All Together: Ancient and Modern Approaches to Joining, Repair and Consolidation, London: Archetype Publishing, Ltd., pp. 113-119.
Menei, E. 2017, ‘Use of East Asian materials and techniques on papyrus: Inspiration and adaptation’ in Adapt & Evolve 2015: East Asian Materials and Techniques in Western Conservation, pp. 118–27.